factory Outlets for Concord Wire Cut Edm Machine - Flat rail CNC lathes for shaft and disc parts metalworking – FOREST
factory Outlets for Concord Wire Cut Edm Machine - Flat rail CNC lathes for shaft and disc parts metalworking – FOREST Detail:
CK6140 CNC lathe is mainly used for finishing and semi-finishing of shaft and disc parts. It can process inner and outer cylindrical surfaces, conical surfaces, turning threads, boring holes, reaming holes and various curved revolving bodies;
The spindle use servo electric elements , low-speed spindle with large torque;
CK6140 has the advantages of high power, good rigidity, large precision reserve, long life, etc. Equipment with high performance and versatility. Using this CNC lathe, as long as the machining requirements of the workpiece are compiled into a machining program according to the specified format, randomly input into the microcomputer, and then through the system keyboard, press the workpiece number and the start key, the lathe will automatically complete the outer circle of the part under the control of the system, inner hole, end face, step, grooving, chamfering, etc., and has automatic turning function of arc, curve, thread and taper.
Features:
1. There are manual, hydraulic and pneumatic options for chuck and tailstock.
2. Both the machine tool guide rail and the saddle guide rail are made of hard guide rails made of special materials. After high-frequency quenching, they are super hard and wear-resistant, durable and have good machining accuracy.
3. The frame has four stations, six stations, vertical and horizontal for selection. It adopts precise end tooth plate positioning, and can also choose row knives, with high repeat positioning accuracy
4. The tailstock has a quick cam clamping device with high working efficiency. There is a device in the tailstock sleeve to prevent the drill bit from rotating, which avoids damage to the taper of the inner hole of the tailstock sleeve due to the rotation of the drill bit caused by misoperation, and effectively protects the tailstock components.
5. The optimized design of the headstock is suitable for the turning of disc and shaft parts. It can process straight lines, arcs, metric and inch threads, and multi-thread threads. It is suitable for turning discs and shafts with complex shapes and high precision requirements. Class parts processing.
6. The numerical control system adopts the well-known brands at home and abroad such as Guangshu system or Kaiendi. It can be driven by hybrid stepping motor or AC servo motor, and other systems can also be selected according to user requirements.
7. The guide rail is equipped with a scraping device to prevent the guide rail from being corroded by iron filings and coolant, and facilitate the cleaning of the iron filings.
8. Easy to operate, especially suitable for the processing of complex parts or high-precision mass parts, and it is also the first choice for CNC teaching.
Product advantages:
1. The machine tool has high precision, and the spindle adopts HRB high-precision double ball bearing support, which has low noise, high precision and good stability.
2. The bed guide rail is finely ground after ultrasonic quenching, with high hardness and good rigidity.
3. The electric four-station tool post adopts precise toothed plate positioning, and the repeat positioning accuracy is high.
4. The tailstock has a quick cam clamping device with high working efficiency. There is a device in the tailstock sleeve to prevent the drill bit from rotating, which avoids damage to the taper of the inner hole of the tailstock sleeve due to the rotation of the drill bit caused by misoperation, and effectively protects the tailstock components.
5. The numerical control system adopts the well-known brands at home and abroad such as Guangshu system or Kaiendi. It can be driven by hybrid stepping motor or AC servo motor, and other systems can also be selected according to user requirements.
6. Easy to operate, especially suitable for the processing of complex parts or high-precision mass parts, and it is also CNC teaching.
Contact with us to know more lathes
CK6140 | CK6150 | CK6180 | |
Max swing diameter over bed(mm) | 400 | 500 | 800 |
Maximum swing diameter on the tool post(mm) | 220 | 280 | 480 |
Max length of workpiece(mm) | 750/1000/1500 | 1000/1500/3000 | 900/1300/1700/2700 |
Wide of guide rail(mm) | 330 | 450 | 600-750 |
X axis travel(mm) | 250 | 265 | 400 |
Z axis travel(mm) | 750/1000/1500 | 1000/1500/3000 | 1500 |
Spindle speed (rpm) | Stepless 150-2500 | 50-1500 | 25-850 |
Spindle hole dia(mm) | Φ 60 | Φ82 | Φ100/130 |
Nos of cutter | 4/6/8 | 4/6 | 4/6 |
Repetition pointing accuracy | 0.01mm | 0.01 | 0.01 |
Feeding speed in X axis | 4000 | 4000 | 4000 |
Feeding speed in Z axis | 6000 | 8000 | 6000 |
Feeding in one cuter | 0.005-100 | 0.005-100 | 0.005-100 |
Processing accuracy | IT6-7 | IT6-7 | IT6-7 |
Roughness | 1.6 | 1.6 | 1.6 |
Tailstock sleeve taper | MT4 | MT5 | MT6 |
Tailstock sleeve dia (mm) | 70 | 75 | 100 |
Tailstock sleeve travel (mm) | 120 | 170 | 250 |
Measure (mm) | 2130/2520/3050x1400x1680 | 2800/3100/4100x1650x1650 | 3600/4100/5600x1600x1780 |
Weight (KG) | 1600/1800/2200 | 2800/3100/5000 | 4400/5100/6000 |
Power | 380V, 3Phase, 50HZ or customized |
Product detail pictures:
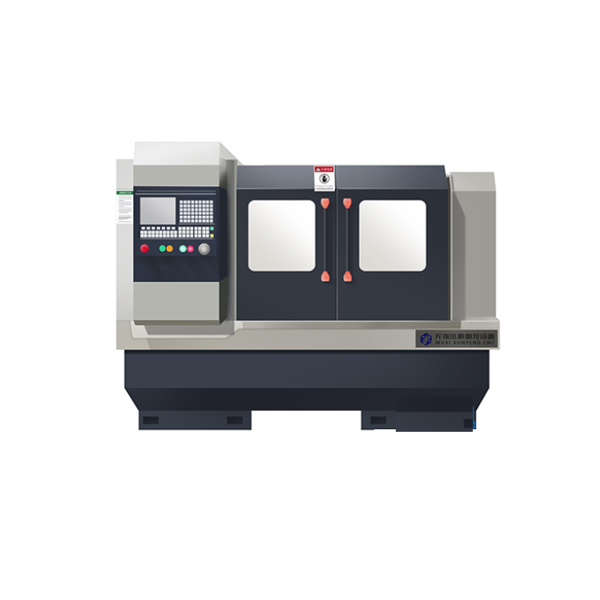


Related Product Guide:
The purchaser fulfillment is our primary focus on. We uphold a consistent level of professionalism, high quality, credibility and service for factory Outlets for Concord Wire Cut Edm Machine - Flat rail CNC lathes for shaft and disc parts metalworking – FOREST, The product will supply to all over the world, such as: Pakistan, Munich, Kenya, As an experienced manufacturer we also accept customized order and we could make it the same as your picture or sample specification. The main goal of our company is to live a satisfactory memory to all the customers, and establish a long term business relationship with buyers and users all over the world.

The factory technical staff gave us a lot of good advice in the cooperation process, this is very good, we are very grateful.
